The problem
No mechanical structure is completely rigid, so when
we were approached by a customer asking for one, we were
a little surprised. A box was needed, to hold optical
components for scanning a distant object in 3D. Because
the technology relies on measuring phase differences in
light, the mechanical structure needed to hold the components
stationary to within a few microns and micro radians.
That’s pretty close to rigid. The product had different
options, so the mechanical structure also had to be modular
and quickly assembled without any special tools. The customer
wanted to improve on an existing carbon fibre model. Coupland
Bell consultants were asked to produce a concept design,
in conjunction with a design agency.
|
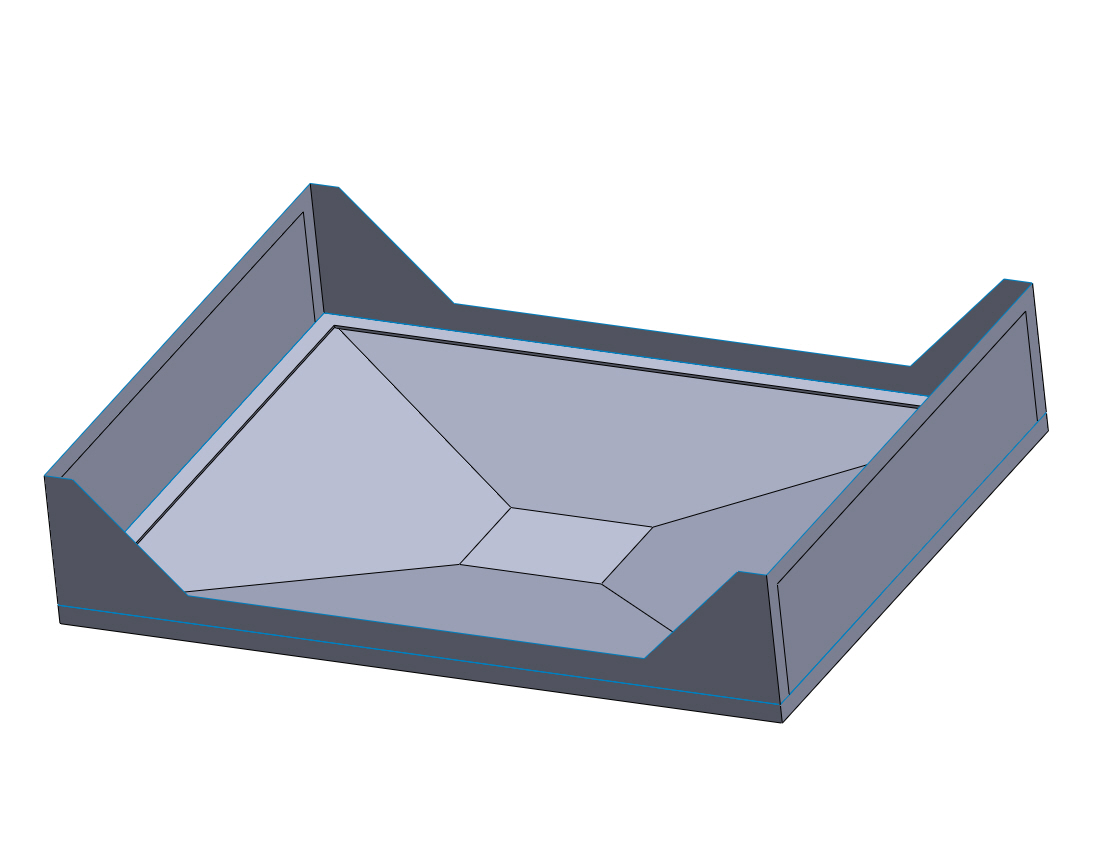 |
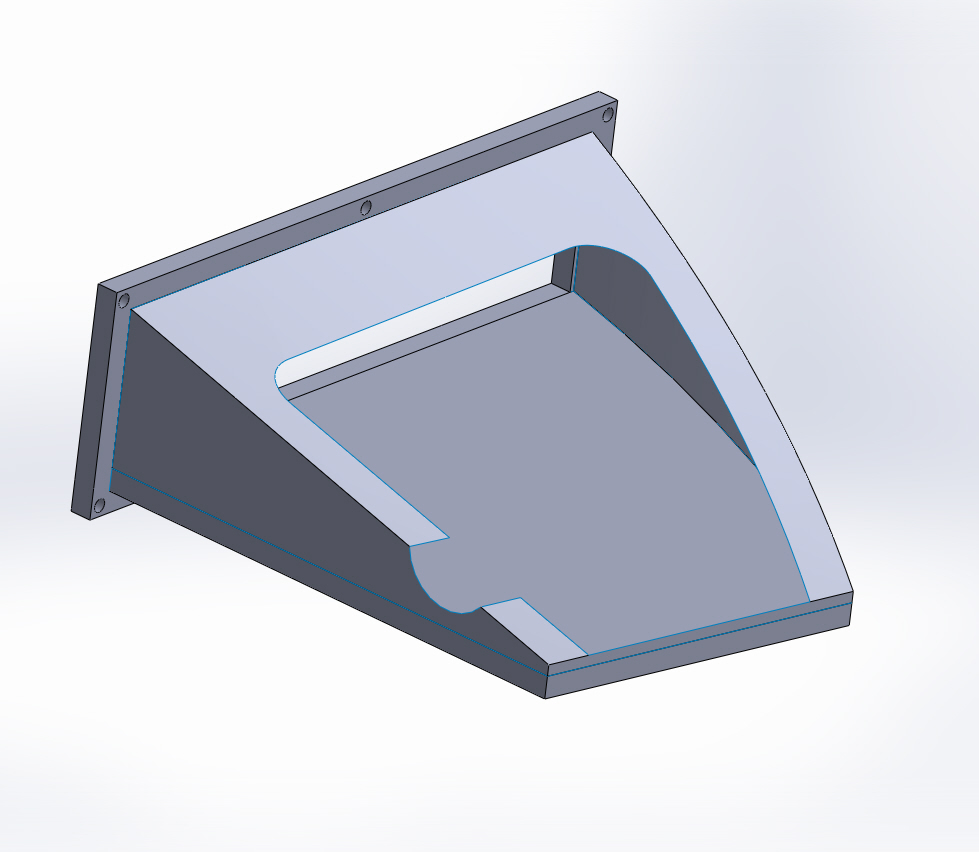 |
Our solution
Carbon fibre was the clear choice for a structure
that would be reasonably light, very rigid and be as thermally
stable as we could reasonably make it. The main problem
was that a projector would be mounted in a central box,
resting on a tripod stand and a camera would be mounted
in a separate module cantilevered from its side. The camera
could be mounted on either side. This aspect of the design
had already been fixed. This made the loads asymmetric with
the supports, introducing a twist that would be hard to
control to within micro radians.
Our consultants solution was to mount the projector
within a cradle. The cradle and camera support would be
separately mounted to a rigid structure on the tripod.
This allowed the projector and camera to move together
under gravity and thermal loads and balanced the twisting
effect. Various different concepts for the mechanical
structures were tried using FEA,
leading to a simple cost-effective solution. For the quick
assembly joints, our consultants modelled dove tails,
fir trees, nested cylinders and tapered joints. The performance
of each was quantified, leading to a table comparing the
performance, advantages and disadvantages of each type,
helping our customer decide which to use.
|