|
Mechanical failure analysis of cracked HDPE moulding
The problem
Rotational moulding in high density polyethylene, HDPE,
can be very cost effective for large mouldings.
It is often used for tanks, street furniture and industrial
casings, as well as marine products. The design
details, particularly structural ribs and reinforcing
features, are heavily constrained by the manufacturing
process. This is because the HPDE enters the mould
as a powder and it gets distributed around the inside
as it is tumbled by the mould. The wall thickness
is not even and may be too thin or thick in corners and
parts of the mould where the material isn't evenly distributed
leading to mechanical failure.
|
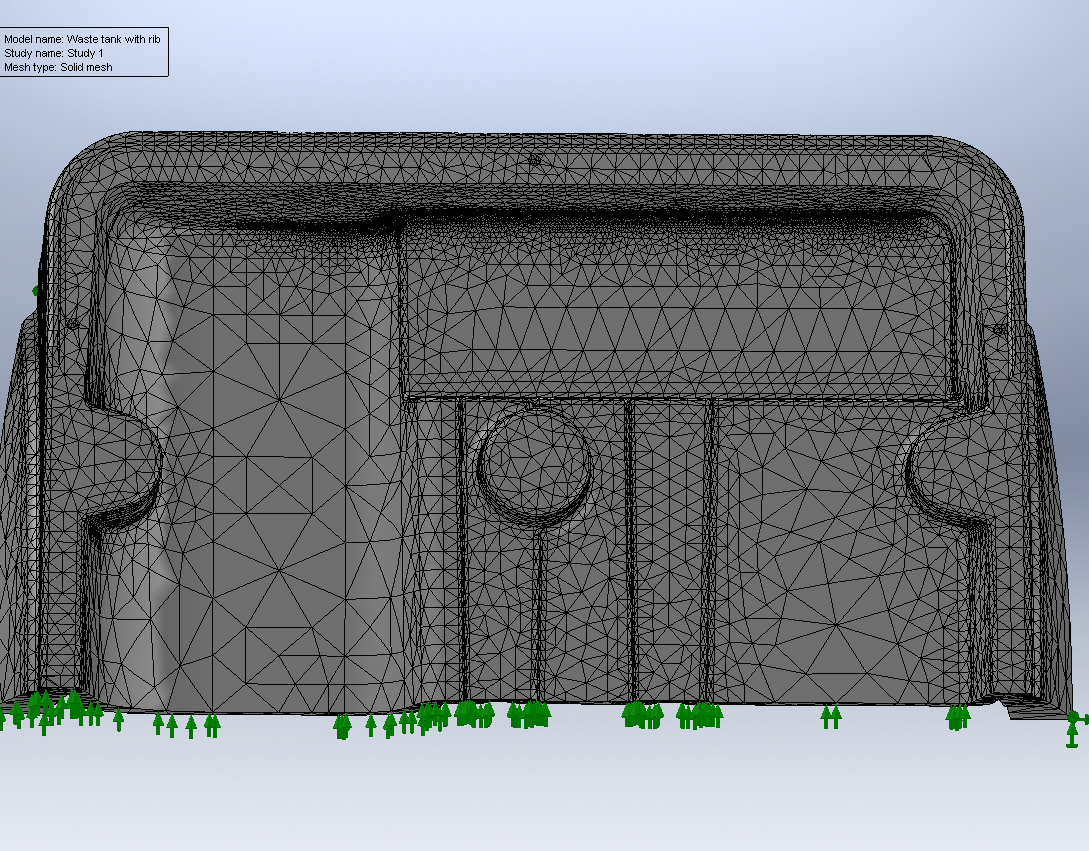 |
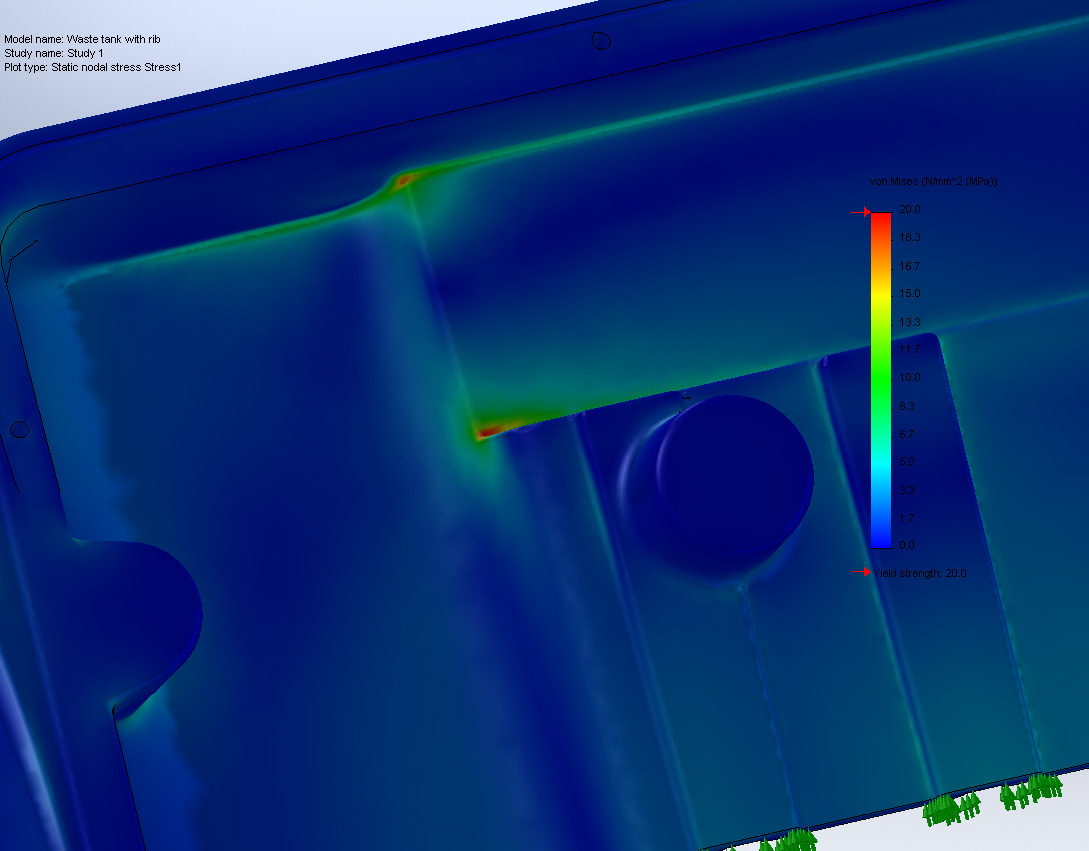
|
Our consultants were approached by a company making casings
for an industrial product, after a casing suffered a mechanical
failure. The casing had cracked along a corner when
the casing had been under a negative pressure.
Our solution
At the outset it wasn't clear whether the mechanical
failure (crack) was a due to a design fault or a manufacturing
fault. Our consultants built a finite
element analysis model of a portion of the casing,
with a fine mesh in the area of the crack. FEA
showed that the casing would not have cracked if it was
the correct thickness and it was unstressed when it left
the factory.
|
|
A sample casing was cut up and this showed that the local
thickness was not correct. Our consultants then
modelled the cooling process and found a high residual
stress at the cracked corner, due to the manufacturing
process. The combination of the residual stress
and incorrect thickness were enough to cause mechanical
failure under negative pressure.
Minor changes to the structural details can often solve
this sort of problem. Metal plates or reinforcing
bars can sometimes be incorporated into rotational mouldings.
In this case, the client took the opportunity to design
an improved product and our consultants assisted with
the structural design of an improved casing, which has
not failed.
|
|